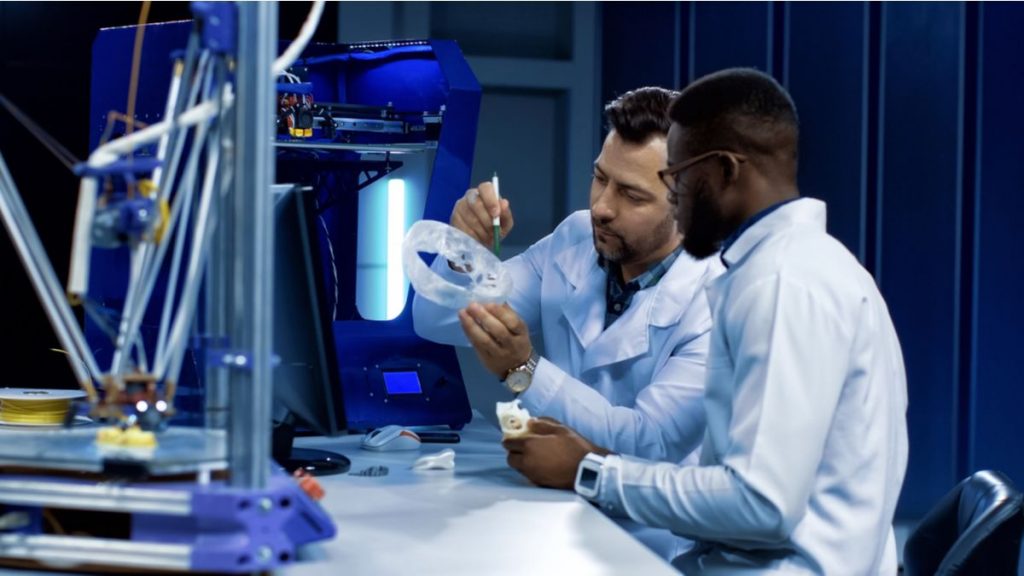
Des ingénieurs américains ont mis au point une nouvelle technique d’impression 3D d’objets métalliques consistant à lier des particules de titane à des vitesses supersoniques. Les métaux obtenus ont la particularité d’être très poreux, ce qui les rend particulièrement indiquées pour la fabrication d’objets biomédicaux tels que les implants et les prothèses articulaires.
Un procédé d’impression 3D innovant
L’impression 3D traditionnelle consiste à déposer couche par couche, à l’aide d’une buse, du plastique, des hydrogels, des cellules vivantes ou d’autres matériaux pour fabriquer un objet. Les pièces et les objets métalliques sont généralement imprimés en 3D d’autres manières, en appliquant un laser sur un lit de poudre métallique afin de faire fondre sélectivement certaines sections pour obtenir la forme souhaitée, ou en projetant à haute vitesse une poudre métallique sur un substrat pour lier les particules entre elles.
Présentée dans la revue Applied Materials Today, la nouvelle technique mise au point par les chercheurs de l’université Cornell, connue sous le nom de « pulvérisation à froid », repose sur une approche similaire. Ici, les scientifiques soufflent des particules d’alliage de titane (mesurant chacune entre 45 et 106 microns de large) à des vitesses allant jusqu’à 600 mètres par seconde (contre 340 m/s environ pour la vitesse du son). Au-delà, ces derniers ont déterminé que l’impact entraînerait une détérioration trop importante des particules, les empêchant de se lier efficacement les unes aux autres.
Les matériaux sont ensuite chauffés et ramollis afin d’améliorer la liaison des particules de titane. Il s’agit une fois encore d’une opération soigneusement contrôlée, impliquant des températures allant jusqu’à 900 °C (sachant que le point de fusion du titane est de 1626 °C). Ce qui permet aux chercheurs d’obtenir un objet métallique doté d’une structure poreuse et s’avérant jusqu’à 42 % plus résistant que des objets similaires fabriqués selon des procédés de fabrication conventionnels.
De nombreuses applications envisageables
« Nous nous sommes concentrés sur la fabrication de structures cellulaires, qui possèdent de nombreuses applications dans la gestion thermique, l’absorption d’énergie et la biomédecine », explique Atieh Moridi, auteur principal de l’étude. « Plutôt que d’utiliser uniquement la chaleur comme force principale pour la liaison, nous utilisons maintenant la déformation plastique pour lier ces particules de poudre métallique ensemble, ce qui se traduit par une structure plus robuste. »
Selon l’équipe, cette nouvelle méthode pourrait permettre de créer des matériaux et objets dans le domaine de la construction, le transport et l’énergie, mais se révélerait surtout adaptée à la création d’implants biomédicaux, en raison de sa structure poreuse constituant un support de choix pour les cellules des patients, ce qui aiderait à reconstruire le tissu naturel et à mieux ancrer l’implant.
« Avec des implants présentant ce type de structures, l’os peut se développer à l’intérieur des pores, formant ainsi une fixation biologique », explique M. Moridi. « Cela permet de réduire la probabilité de détachement du dispositif. Ce qui constitue aujourd’hui un problème, avec de nombreux patients devant subir des opérations chirurgicales supplémentaires afin de retirer l’implant parce que celui-ci s’est desserré et cause d’importantes douleurs. »
Par Yann Contegat, le
Source: New Atlas
Étiquettes: implant, titane, impression 3D, prothese, biomedical
Catégories: Technologie, Actualités